Quality: Been There. Tried That!
One of the more challenging issues with which I deal is the people component of the People-Process-Technology trilogy. Any consultant that impacts the culture of an organization will admit the people component is the most difficult.
So, it will come as no surprise that one of my greatest challenges in dealing with IT is the experience some IT people may have had with “QUALITY”. I often hear something like, “Quality, Smaulity. We tried it and it didn’t work.” OK, so Total Quality Management (TQM), Six Sigma, ITIL, and perhaps Kaizen have sometimes earned bad reputations. But this is often because some organizations look to these initiatives only for short-term gain. They then fail to integrate the concepts of these proven methodologies into the way they do business.
All the big three automotive manufacturers have used Six Sigma and other “improvement” and “quality” initiatives. But ask yourself why Toyota or Honda is doing so well in the marketplace. Is it only the effect of lower cost production capabilities? Or, is it something else? Toyota adopted the quality concepts of Shewhart, Deming and others and incorporated them into the very fabric of their organizations. The Toyota Production System (TPS) is part of Toyota’s culture. It influences every decision. It is not just part of the manufacturing process but an instrumental component of the way they do business. In TPS, quality is not a point solution put in place to resolve an isolated issue, but a way business is conducted. This raises improvement from a utility or even as a governance guideline to being a critical part of the culture.
Some say that even if an improvement effort worked it never really “stuck”. Well, I agree. There’s is no reason to improve a process if it isn’t going to “stick”. Why spend the time, money and resources fixing something if it’s not going to last? Just accept the fact that your process is broken. Then you may devote all your time REACTING to situations. However there is a better way. Once you have established the improvement, design a control plan (see figure).
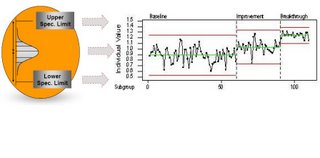
The control plan, the output of the final step of the Six Sigma DMAIC process, provides the means to:
• Prevent “backsliding”
• Preserve the project investment
• Empower process owners
• Ensure the process indicators are reported and matured as the process matures
• Design reports that meet the needs of specific customers
• Nurture the “Learning Organization” for cultural change
Quality WILL work. The concepts upon which our modern improvement methodologies are based are over 50 years old. Their legacy is proven. And improvements can have lasting impact. Organizations need first to accept the cultural implications. They then need to ensure the improvement stays in place by applying the common sense principles of a control plan.
0 Comments:
Post a Comment
<< Home